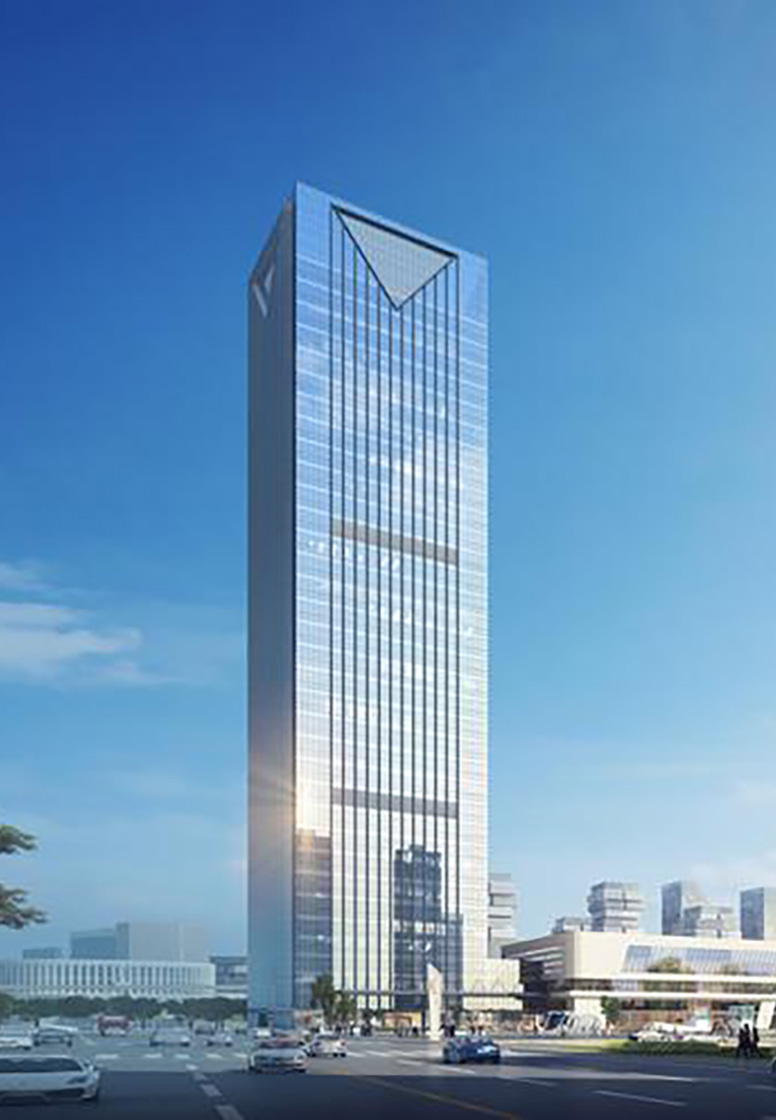
濰坊華光高科電子有限公司 Weifang Huaguang High tech Co., Ltd
濰坊華光高科電子DO30系列數字式三用表校驗儀,多功能校準儀,交直流標準源,單三相功率源,繼承了濰坊華光電子有限公司,濰坊華光電聲儀表有限公司,濰坊華光電子集團公司儀器廠,濰坊計算機公司儀器廠,濰坊市無線電八廠,經過潛心研究開發出的DO30系列數字式三用表校驗儀,XF30系列多功能校準儀的生產經驗技術,于2001年11月,正式組建濰坊華光高科電子有限公司.華光高科繼續以“拼搏奉獻,為中華爭光”的精神致力于數字式三用表校驗儀,多功能校準儀,交直流標準源等電子計量測試校準儀器儀表的研發生產.公司坐落于代表濰坊科技發展的華光電子集團總部,是濰坊市的高新技術企業.華光高科電子專業生產DO30系列,數字式三用表校驗儀、多功能校準儀、交直流標準源,單三相功率源.華光DO30已有盡50年的生產制造歷史.華光生產的HG30三用表校驗儀、多功能校準儀、交直流標準源已經是全國計量校準,質檢部門,萬用表,電流表,電壓表,功率表,校驗儀,校準儀器的重要選擇。 濰坊華光高科電子有限公司擁有一批高素質的人才隊伍,軟、硬件設計開發人員占公司總人數的85%,碩士、博士生占設計開發人員的80%以上。擁有一批高層次的專業技術人員和管理人員,公司為他們創造了一個發揮聰明才智、實現人生理想的平臺,海闊憑魚躍,天高任鳥…
我們的簡介
我們是一家集生產、銷售和服務于一體的企業
我們的產品
三用表校驗儀、多功能校準儀、交直流標準源、單三相功率源等
我們的實力
我們擁有完整的服務管理系統和設備,以確保及時交付
聯系我們
我們將竭誠為您服務,保證售后服務
產品展示
多年三用表校驗儀、多功能校準儀、交直流標準源、單三相功率源等提供一站式解決方案
產品分類
HUANG GUANG
華光品質 創想未來 攜手共創
高品質儀器專業制造商
0536-8222888 13806491159